Quality control in forming and stamping technology with iQ-eye
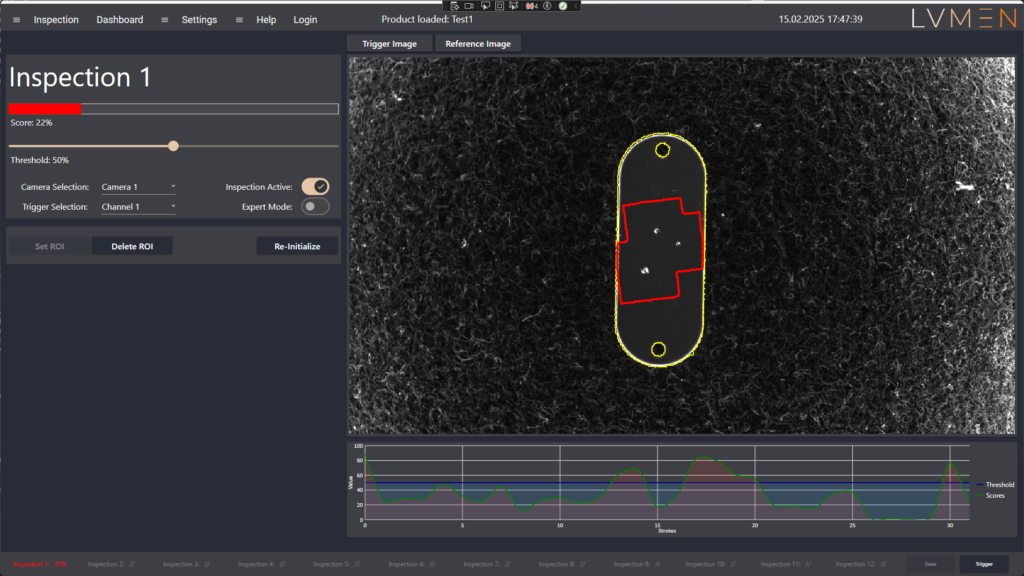
In this case, the iQ-eye is used as a quality inspection system in forming and punching technology. The produced parts are transferred to the outfeed conveyor where they are inspected for quality defects by the iQ-eye. The iQ-eye is positioned above the outfeed conveyor with an illumination unit and image acquisition is triggered by a sensor or system signal.
A total of up to 6 parts can be monitored simultaneously with one system. Previously, 6 individual stand-alone systems had to be installed in such situations. The iQ-eye reduces this cost-intensive redundancy to a single system.
The parts are automatically checked for surface defects or contour errors. Scratches, cracks, holes and other quality defects are thus reliably detected.
A particular challenge for quality inspection systems in forming and stamping technology is the frequent recipe changes. It is not unusual for several different parts to be produced in varying batch sizes within 24 hours. A quality inspection system must therefore be able to react to this variance with minimal user interaction.
The iQ-eye fulfills this task. Thanks to the integrated AI, a new part can be created quickly and taught in within a few minutes. Without any order preparation on the office PC. Only 15 good parts are required to teach in new recipes.
The images of all recorded parts are automatically saved and labeled (good/bad) so that they can be evaluated for later analysis.
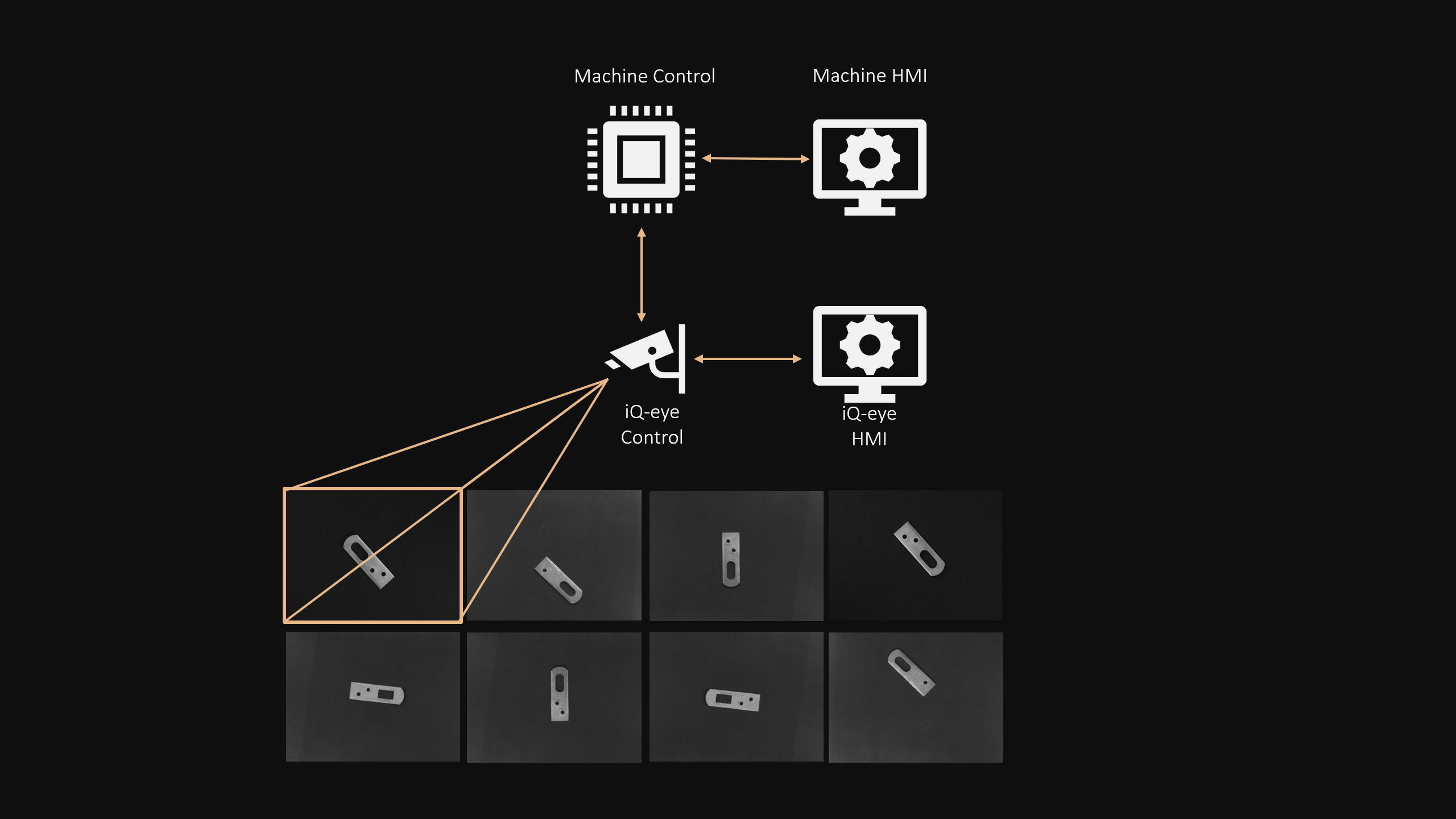